Setting up a press brake machine for optimal performance requires a combination of precise programming and meticulous attention to detail. In this blog, we will explore the best practices that can help you achieve accurate bends and enhance productivity while ensuring safety.
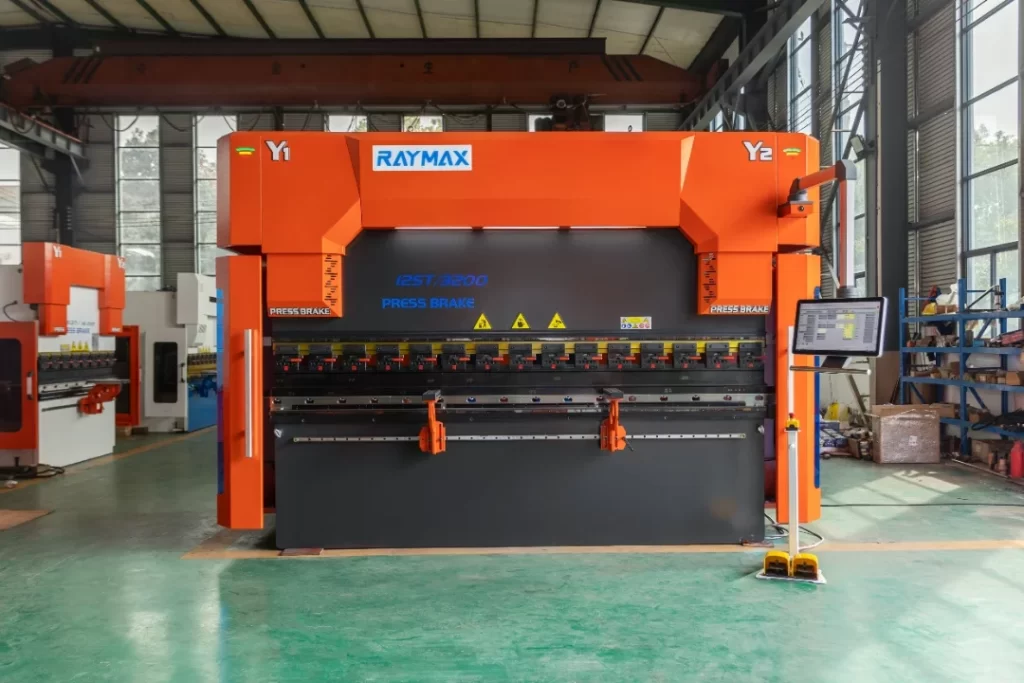
Material Understanding:
Before programming the press brake, thoroughly understand the characteristics of the material you are working with. Factors such as material type, thickness, and elasticity influence the bending process. Conduct material tests and consult material charts to determine the appropriate tonnage, tooling, and bending parameters.
Tooling Selection and Maintenance:
Choose the right tooling based on the material and desired bend angles. Ensure that the punches and dies are properly aligned, securely mounted, and free from wear or damage. Regularly inspect and maintain the tooling to prolong its lifespan and ensure consistent bending results.
Accurate Programming:
Precise programming is crucial for achieving accurate bends. Utilize software programs or dedicated press brake controllers to input the correct bend angles, dimensions, and sequencing. Take advantage of features like automatic bend allowance calculations to streamline the programming process.
Machine Calibration and Setup:
Regular calibration of the press brake machine is essential to maintain accuracy. Calibrate parameters such as ram speed, stroke depth, back gauge position, and crowning (if applicable) based on the material and bend requirements. Properly adjust the machine's mechanical stops and back gauge fingers to prevent over-bending or under-bending.
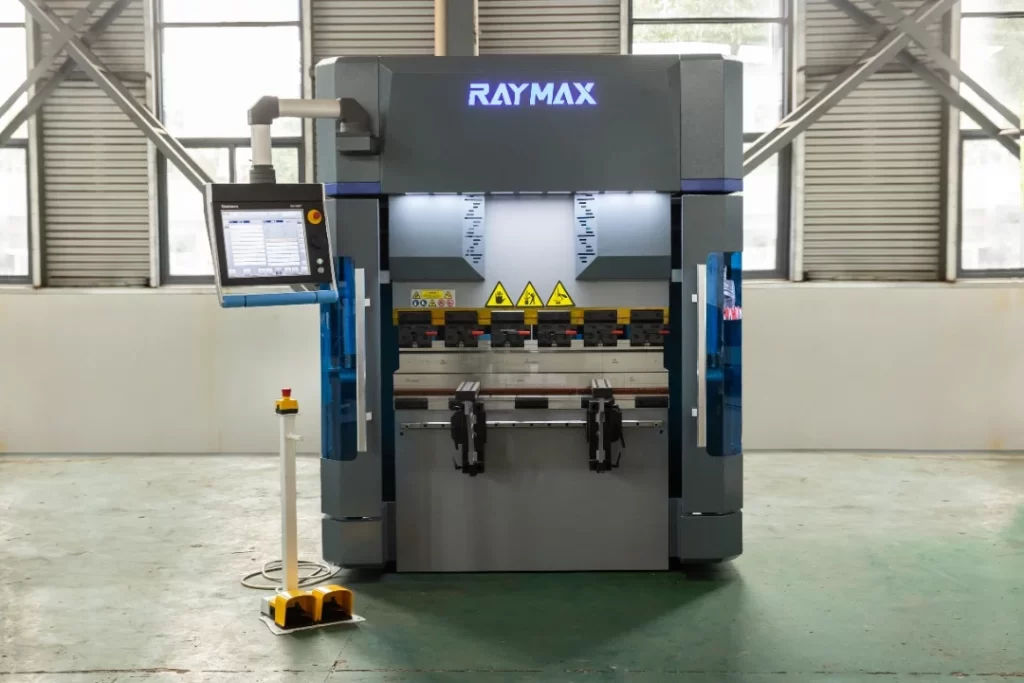
Test Bends and Adjustments:
Perform test bends to validate the programming and machine setup before starting production. Use scrap material to simulate actual production conditions and verify bend angles, dimensions, and tolerances. Make necessary adjustments to the programming or machine settings based on the results of the test bends.
Safety Procedures:
Prioritize safety during press brake setup and operation. Provide comprehensive training to machine operators on safe operating procedures, including proper handling of heavy materials, tooling, and machine controls. Implement safety features such as light curtains, two-hand controls, and emergency stop buttons to minimize accidents.
Ongoing Maintenance and Monitoring:
Regularly inspect and maintain the press brake machine to ensure optimal performance. Lubricate moving parts, check hydraulic system pressures, and inspect electrical connections. Monitor the machine for signs of wear or damage and address any issues promptly to avoid unplanned downtime.
Continuous Improvement:
Encourage a culture of continuous improvement by collecting and analyzing data on machine performance, setup times, and quality control. Identify areas for optimization, such as reducing setup times or improving bend accuracy, and implement solutions to enhance productivity and efficiency.
By following these best practices for programming and setting up your press brake machine, you can achieve precise bends, improve productivity, and maintain a safe working environment. Remember to understand your materials, select and maintain proper tooling, program accurately, calibrate the machine, perform test bends, prioritize safety, and regularly maintain and monitor your equipment. With these practices in place, you'll be well on your way to success in metal fabrication with your press brake machine.