Press brake machines are essential tools in metal fabrication, offering precise bending capabilities crucial for various industries, from automotive to aerospace. One critical aspect that significantly impacts their performance is the selection of the right tooling options. In this comprehensive guide, we will delve deep into the realm of press brake tooling, exploring different types, considerations, and best practices to enhance efficiency and quality in metal bending operations.
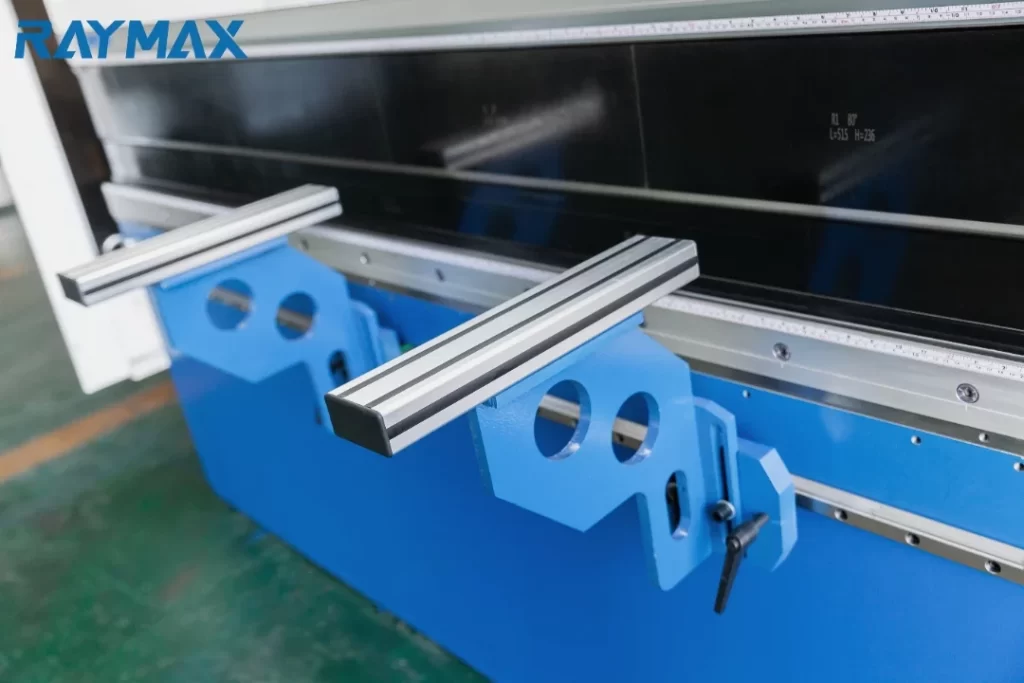
Unveiling the World of Press Brake Tooling
Press brake tooling encompasses the components utilized to shape and bend metal sheets. These tools come in a myriad of shapes, sizes, and materials, each playing a distinct role in the bending process. Common types of press brake tooling include punches, dies, and adapters, working in harmony to achieve precise bends and shapes with accuracy and consistency.
Exploring Different Types of Press Brake Tooling
1. Punches:
Punches serve as the upper tools that apply force to the metal sheet, inducing bending or forming. Available in various profiles like V-shaped, U-shaped, and radius punches, each type is tailored to specific bending requirements. Opting for hardened and ground punches ensures durability and precision, guaranteeing reliable performance across multiple bending operations.
2. Dies:
Dies act as the lower tools that impart the desired shape to the metal during bending. Similar to punches, dies come in diverse profiles, including V-dies, acute angle dies, and hemming dies. Selecting the appropriate die profile is crucial for achieving accurate bends and minimizing material distortion, ensuring high-quality results in metal fabrication.
3. Adapters:
Adapters are supplementary components that expand the capabilities of press brake tooling. They encompass accessories like safety rails, crowning systems, and hydraulic clamping systems, enhancing productivity, safety, and versatility in bending operations. Integrating adapters into the tooling setup elevates efficiency and flexibility, catering to a broader range of bending requirements.
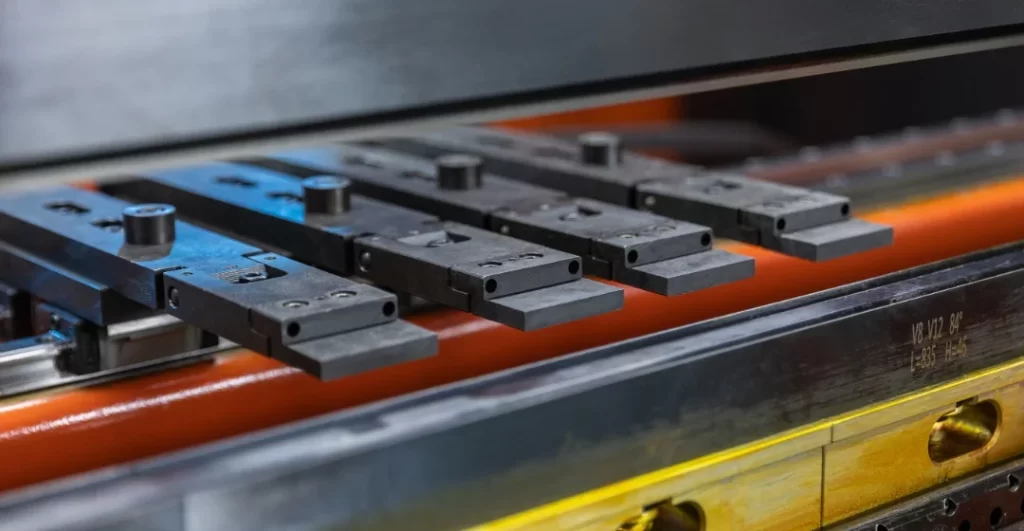
Key Considerations in Selecting Press Brake Tooling
1. Material Compatibility:
Choosing tooling materials that align with the metal being bent is paramount for achieving superior results. Common materials such as tool steel, carbide, and high-strength alloys offer distinct advantages in terms of durability and wear resistance, ensuring longevity and optimal performance in bending operations.
2. Bending Applications:
Considering the specific bending applications and project requirements is essential when selecting press brake tooling. Factors like bend angle, material thickness, and production volume play a pivotal role in determining the ideal tooling profiles and configurations to meet the demands of each project effectively.
3. Machine Compatibility:
Ensuring that the chosen tooling options are compatible with the specifications and capabilities of your press brake machine is crucial for maximizing performance and preventing equipment damage. Factors such as tonnage capacity, bed length, and tooling mounting systems should be taken into consideration to optimize bending operations and ensure seamless integration with the machine.
Best Practices for Tooling Maintenance and Optimization
1. Regular Inspection:
Conducting routine inspections of press brake tooling to identify signs of wear, damage, or misalignment is essential for maintaining accuracy and prolonging tooling lifespan. Timely intervention and maintenance help uphold performance standards and ensure consistent results in metal bending operations.
2. Proper Storage:
Storing press brake tooling in a clean, dry environment is crucial to prevent corrosion and damage. Utilizing protective coatings or packaging when the tooling is not in use helps preserve tooling surfaces and prolongs their longevity, ensuring optimal performance in subsequent bending tasks.
3. Lubrication:
Applying lubricants as recommended by the manufacturer is vital to reduce friction and wear during bending operations. Proper lubrication enhances tooling performance, minimizes wear and tear, and extends the service life of the tooling components, contributing to long-term efficiency and productivity in metal fabrication processes.
Selecting the right tooling options is a pivotal step in optimizing the performance and efficiency of press brake machines in metal fabrication operations. By familiarizing yourself with the various types of tooling, considering key factors in selection, and adhering to best practices in maintenance and optimization, you can achieve consistent, high-quality bends while maximizing productivity and profitability in your metal fabrication endeavors.
Investing in quality press brake tooling is not just an acquisition of tools; it is an investment in the success and growth of your metal fabrication business. Whether you are fine-tuning your punch and die combinations or exploring advanced adapters for specialized applications, the right press brake tooling choices can pave the way for enhanced precision, efficiency, and excellence in your metal bending operations.